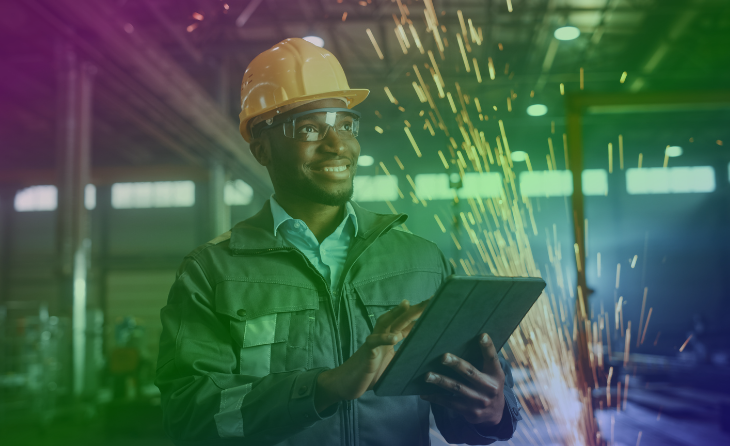
The manufacturing industry is undergoing a huge transformation to Industry 4.0. To help optimise this, manufacturers need to ensure resilience is at the heart of the business and that they are able to safeguard production output and mitigate threats from cyber crime and supply chain issues.
Furthermore, today’s manufacturers operate amid frequent supply-chain disruptions, having a business continuity and disaster recovery plan in place is essential to not only remediate a critical event as it happens, but to ensure products continue to reach and be delivered to customers.
Drawing on our extensive experience collaborating with manufacturers, we have developed an acute understanding of the challenges that this industry encounters and we acknowledge the central importance of technology in effectively tackling these challenges.
This guide outlines four essential business continuity strategies tailored specifically for the manufacturing sector, ensuring resilience and success in the face of change.
1. Identify the risks your business may face
The first step is to understand what in your business is critical, what those critical things depend on, and how long you can be without them for. In conjunction with this, by understanding the recovery capabilities of those dependent things, you will start to build a picture of where the risks to your recovery and business are. All of this information can be identified by performing a Business Impact Analysis (BIA). In the manufacturing world, the most common disruptions are usually hardware and software problems, power failures, cybercrime, human error, natural disasters and fires.
Performing a BIA can be hard work and time consuming, but it can be a great fast-track tool for identifying operational risks that might not otherwise surface except at time of incident. If you have the resource, you can conduct a BIA internally, however, many businesses choose to outsource this.
2. Identify your business-critical resources
Office buildings, warehouses, production lines, transportation – these are just a few of the key assets manufacturers own and operate. All these assets are vulnerable to threats and disruptions, so it is important that your business continuity and disaster recovery team(s) sit down with senior leadership to evaluate which resources are most critical to the business.
It doesn’t need to be a work of literature, a simple list of the business-critical assets that must be safeguarded at all times will be suffice. Once you have this you can evaluate which business functions will need to be restored first in order to protect these assets.
Whether your business chooses to prioritise equipment, IT systems of production lines, the key is to recognise what is most important for the businesses, once you have identified your business-critical resources, it’s time to build your business continuity and disaster recovery plans.
3. Build your business continuity and disaster recovery plans
Now it is time to build your business continuity, crisis management and disaster recovery plans – it’s important to know the differences between these plans and how these can complement one another.
A crisis management plan enables a business to react quickly in a structured way to any unplanned or sudden incident by providing critical information around communications to staff and key stakeholders, escalation and stand down procedures as well as immediate actions. A business continuity plan sets out the requirements to recover and resume critical operations to a predefined level following any disruption that impacts on the way the business operates, for any length of time. A disaster recovery plan is predominantly concerned with the recovery of the business’ critical technology and provides procedures for managing the recovery of IT and communication services and supporting the business following disruption of these services. A crisis management plan can be part of a business continuity plan if required.
Top tip – plan smart, not big!
Over the years, we have seen many organisations try to plan for just about every possible eventuality. But in reality, it simply isn’t possible to plan for everything that ‘might’ happen – so don’t try to!
A good plan isn’t one that tells you what to do in a specific scenario, but one that helps and supports you in making informed decisions for ‘any’ scenario. A good plan is one that will be used because it is helpful, so consider when you create your plan(s) what information is vital in helping you make those decisions. Anything else probably isn’t required, it just makes the plan unwieldy and unusable. If you feel you need a plan that is for a specific scenario, make sure it only focusses on that scenario and most importantly, make sure that people understand its purpose.
4. Leverage outside resources
No one is immune from cyber threats, operational risks and Sod’s law! When the worst happens, having a tested business continuity plan and robust business continuity services in place, will make a significant difference to manufacturers. Daisy delivers in both areas, so let us give you some help.
Because business continuity is a complex task, it’s not surprising that many companies look to outsourced solutions. This ensures that you get the benefit of people who are experienced in drawing up business continuity plans. It also means that you have access to best practice solutions.
Our BCM consultants can manage your entire business continuity management programme for you – removing all the challenges of managing business continuity in-house.
Conclusion
In the face of a rapidly changing landscape, the strategic approaches outlined above provide a roadmap for manufacturers to navigate uncertainties with resilience and assurance.
By diligently evaluating potential risks, safeguarding critical resources, and formulating comprehensive business continuity plans, manufacturing businesses can not only withstand unexpected disruptions but also maintain a consistent flow of services to their customers.